Wheel design for precision cycling line
Nov 02,2024
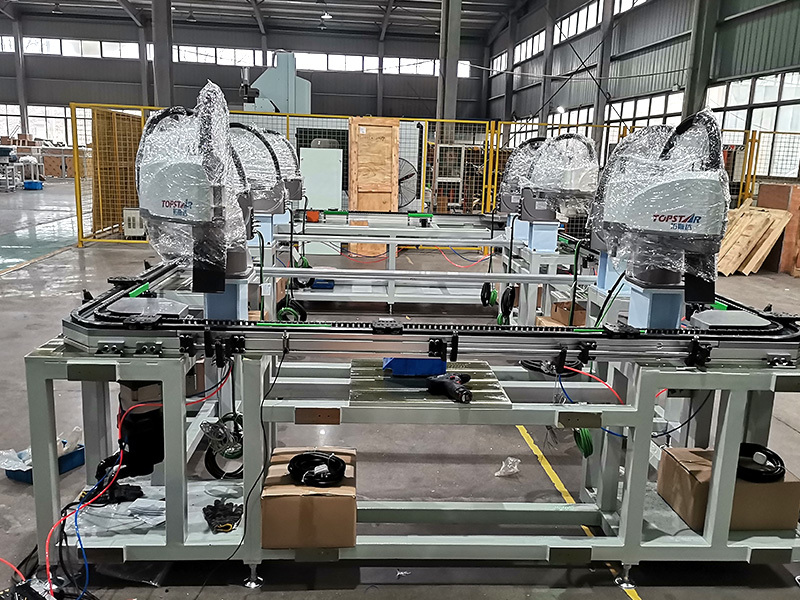
1. Design of the number of teeth for precision circulation line of synchronous belt
The design of the number of teeth needs to comprehensively consider the distance between different ring rails and different trolleys, as well as the reservation for tensioning. This is particularly critical in the design of long lines. The appropriate choice of the number of teeth will affect the transmission ratio and the smoothness of the transmission. Generally speaking, for the reduction transmission, the gear ratio u (z2/z1) is recommended to be 6 to 8, so as to ensure smooth transmission and high efficiency. By rationally planning the number of teeth, the wheel set can operate stably under different working conditions, laying the foundation for the operation of the production line.
2. Design of the shaft
The shaft bears a large force in the wheel set, so its design is crucial. The failure of the shaft must be considered during the design, including the size of the shaft diameter, the elimination of stress, and the tolerance of the fit. First, the size of the shaft diameter should be calculated according to the actual load conditions to ensure that it will not deform or break due to excessive force during the working process. Secondly, the fatigue life of the shaft can be improved by eliminating stress through reasonable heat treatment and machining processes. The design of the fit tolerance should ensure that the connection between the shaft and other components is tight and reliable, and at the same time easy to assemble and disassemble.
3. Selection of bearings
Since the wheel set will be subjected to lateral force in the precision circulation line, the selection of bearings usually requires more margin to cope with this lateral force. When checking the bearing, the radial/axial clearance changes caused by the load and the increase in bearing temperature caused by high-speed rotation should be considered. For the matching design, the matching size selection when the bearing temperature rises and the matching size selection when the load causes the clearance to increase should be considered. Only by selecting suitable bearings and performing correct verification and matching design can the stable operation of the wheel set be guaranteed.
4. The role of the end cover
The end cover may be repeatedly selected or omitted in the design due to concentricity and force problems. Poor concentricity of the wheel set will lead to inaccurate initial positioning, which in turn affects the positioning accuracy of the slide trolley. Therefore, the design of the end cover needs to fully consider the concentricity of the wheel set to ensure that the slide trolley can be accurately positioned. A good end cover design can improve the accuracy and efficiency of the entire production line.
5. Wheel set concentricity
Concentricity refers to the degree of coaxiality of the axes of the two cylinders, that is, the degree of no deviation. In the precision circulation line, the concentricity of the wheel set is crucial. Concentricity can be measured by a micrometer or a three-dimensional coordinate measuring machine. If the wheel set is not concentric enough, it may cause the slide trolley to move left and right during secondary positioning, seriously affecting the accuracy and efficiency of the production line. Therefore, the concentricity of the wheel set must be strictly controlled during the design and manufacturing process.
6. Wheel set material and heat treatment
The material and heat treatment method of the sprocket will have an important impact on its performance. For example, after carburizing, quenching and tempering of 15 and 20 steels, the tooth surface hardness can reach 50-60HRC, which is suitable for sprockets with impact loads. Reasonable selection of materials and heat treatment methods can improve the strength, wear resistance and service life of the sprocket, thereby ensuring the performance of the entire wheel set.
Hot Tags:
Related News